 |
сторінка студента
|
|
|
|
НДРС
Процес перемішування рідини в замкнутому об'ємі є складним фізичним явищем. Для того, щоб проаналізувати це явище щодо конкретного технологічного завдання представляється доцільним використання певних критеріїв, які дозволяють виконати порівняльні оцінки макро- і мікрорівнях. В рамках оцінки ефективності перемішування певного об'єму рідини найчастіше використовуються інтегрований показник «інтенсивність перемішування». Інтенсивність перемішування металу в ковші представляється дуже важливим технологічним показником при обробці стали на установці ківш-піч. По-перше, інтенсивність перемішування металу визначає тривалість деяких етапів обробки, зокрема гомогенізації металу по хімічному складу і температурі або процесу рафінування металу шлаком. По-друге, процес перемішування металу газом відбувається достатньо складно, і в рідкій ванні утворюються як зони інтенсивної циркуляції, так і «застійні області», прояв яких може негативно відбиватися на кінцевих показниках обробки в цілому. По-третє, використання аргону як субстанція, яка забезпечує процес перемішування, допускає додаткові витрати на обробку і відповідно зменшення кількості аргону їх, що використовується, знижує. Основні завдання фізичного моделювання щодо справжньої роботи можна сформувати таким чином: - вивчення особливостей перемішування рідини в ковші при її продуванні газом через пористі блоки, встановлені в днищі; - вивчення можливості оптимізації основних робочих параметрів вдування газу (інтенсивність, кількість продувочних блоків, розташування продувочних блоків і т.п.) для забезпечення процесу перемішування раціональної інтенсивності; - вивчення особливостей перемішування металу з шлаком в процесі продування металу газом.
Фізичне моделювання
Фізичне моделювання процесів перемішування рідини найпереважніше при збереженні однакових геометричних розмірів досліджуваного агрегату і моделі. Проте, об'єм основної маси сталеразливочних ковшів, які використовуються в металургійному виробництві, складає 10-45 м3 (при масі металу 80-350 т), що робить дуже скрутною техніку моделювання із збереженням геометричних розмірів, оскільки це пов'язано з великою трудомісткістю дослідницьких робіт і не завжди гарантує отримання абсолютно надійних даних по фізичному моделюванню. Враховуючи той факт, що при вдуванні газу в рідину вельми важливими представляються процеси, що відбувається під дією сил тяжкість, яка визначає спливання пухирців газу, і сил інерції, які визначають розвиток системи циркуляційних потоків в рідкій ванні ковша, в справжній роботі як базові критерії подібності був прийнятий критерій Фруда і критерій гомохронності. Фізичне моделювання процесу перемішування розплаву інертним газом в ковші виконане на прозорій моделі, що дозволяє візуалізувати всі основні процеси, які відбуваються при продуванні рідини. Геометричні розміри місткості, яка імітує сталеразливочний ківш, були вибрані наступними: діаметр - 0,24 м, висота - 0,40 м. При цьому передбачалася, що вибрана місткість забезпечить моделювання процесів перемішування для ковшів різної конструкції (в першу чергу, відносини висоти наливання металу до діаметру ковша). При цьому як моделююча рідина використовували воду при температурі 18-25оС. Вибір у води як моделююча рідина пояснюється тим фактом, що значення в'язкості води і сталі в області температур позапічної обробки достатньо близькі один до одного. Перемішування рідини здійснювали стислим повітрям. Для імітації шлаку, розташованого на поверхні металу, використовували масло силікону, яке, як відомо, має високі значення поверхневого натягнення, а в'язкість може варіюватися в достатньо широких межах залежно від його температури. Щільність вибраного масла силікону склала 965 кг/м3. Геометричний масштаб фізичних моделей визначався з урахуванням критеріїв подібності Фруда і гомохроності і склав 1:8 і 1:12 по відношенню до вибраного модельованого об'єкту - установка ківш-піч місткістю 60т і 110т відповідно. Для візуального спостереження газорідинних потоків стінки моделей виконували з прозорого скла, а воду підфарбовували спеціальним індикатором для колірної відмінності від масла силікону. Спостережувані картини перемішування фіксували за допомогою цифрової відеокамери. Експериментальні установки дозволили регулювати витрату газу і змінювати положення продувочних пристроїв щодо вертикальної осі судини. В процесі дослідження було знято близько 250 фотографій процесу перемішування для різних значень витрат і швидкостей вдуваного газу, які змінюються в інтервалі 0,1-0,8 м/с.
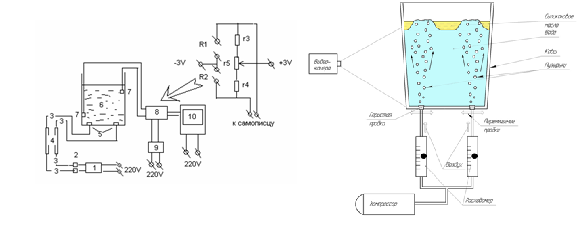
Рис.1 - Схеми фізичних моделей для вивчення процесу перемішування: а - для візуалізації процесів перемішування; б - для оцінки інтенсивності перемішування в ході продування: 1 - компресор, 2 - вузол регуляції подачі повітря, 3 - трубопровід, 4 - блок вимірювання параметрів вдуваного повітря (витрата, тиск),5 - продувочные вузли, 6 - модель ковша, 7 - датчики вимірювання электропроводимости води, 8 - мостова схема, 9 -стабилизированний блок живлення, 10 - самописець
Таким чином, на підставі виконаних спостережень характеру руху потоків у верхній частині ковша основні гідродинамічні потоки можна умовно класифікувати на 5 інтегрованих підобластей з однаковими умовами (напрям векторів швидкостей, величина швидкості, інтенсивність турбулентності) область висхідного газорідинного потоку, проникаючого через шаруючи масла (шлаку); область виходу вдуваного газу в атмосферу, включаючи розбризкування шлаку і металу (тобто область плями виходу газу на поверхню ковша); область низхідних потоків металу, які ковзають уподовж шару шлаку зверху вниз; область горизонтальних потоків металу (з деякою кількістю пухирців газу), які рухаються уздовж поверхні шлаку по напряму від висхідного потоку до периферії ковша; область формування суміші металу, шлаку і пухирців вдуваного газу, яка формується під шлаковим шаром в зоні руху висхідних потоків. Розвиток і розміри тією або іншою з виділених підобластей залежать від ряду чинників, головною з яких є витрата вдуваного газу, кількість продувочних вузлів і їх розташування, а також в'язкість шлаку
|
|